Understanding Production SLA: A Key Element in Effective Business Operations
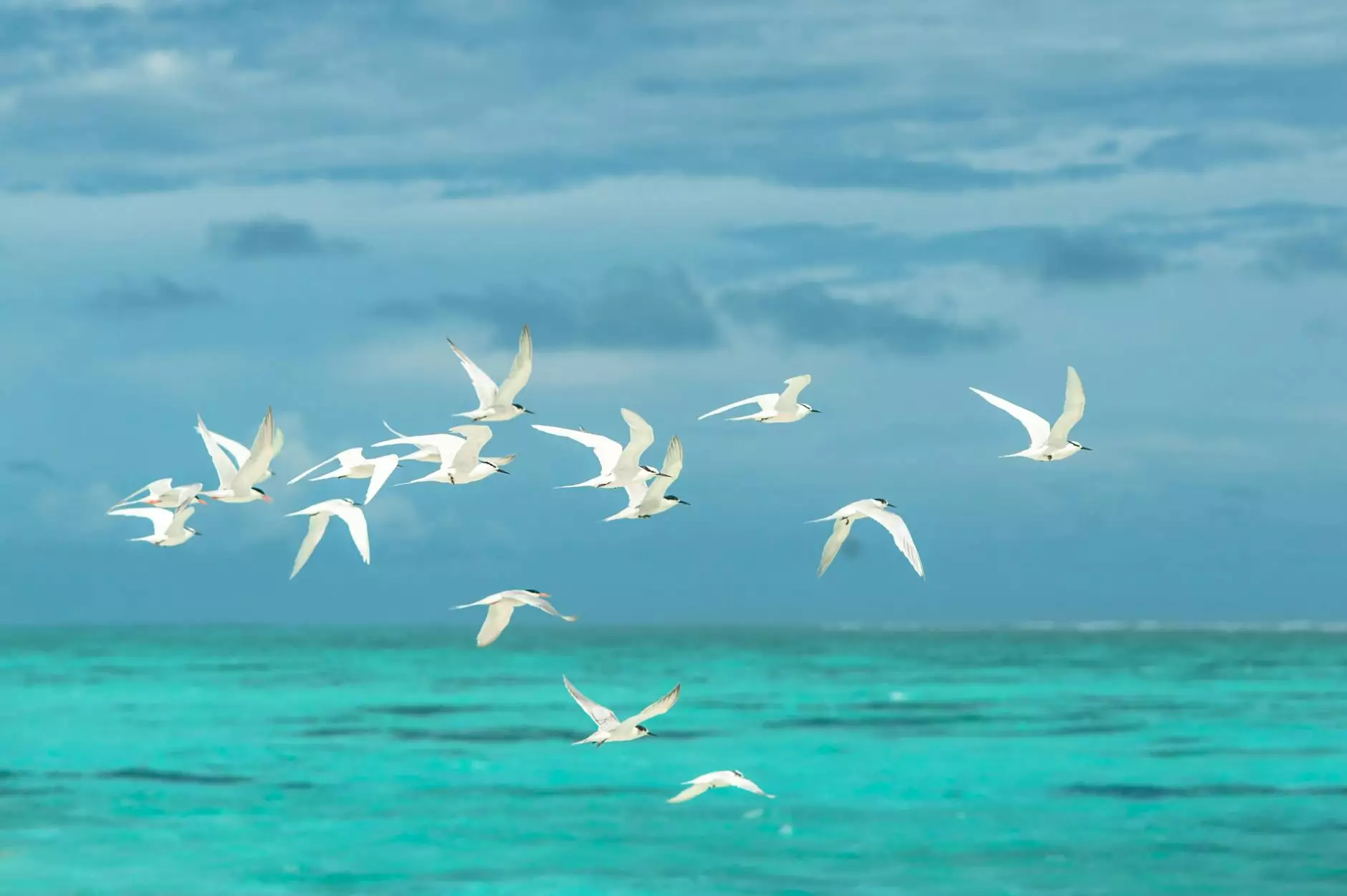
In today’s fast-paced business environment, it is crucial to establish clear benchmarks that define the quality and efficiency of services provided. One such benchmark is the Production SLA (Service Level Agreement). This document serves as a contract between service providers and clients, establishing expectations and accountability in various business domains, including Art Supplies, Product Design, and 3D Printing. In this article, we will delve deep into the nuances of Production SLAs, their significance, and best practices for maximizing their effectiveness to achieve superior business outcomes.
What is a Production SLA?
A Production SLA outlines the specifics of the services to be delivered, including quality metrics, performance standards, and responsibilities of both the provider and the client. This agreement not only serves to clarify expectations but also establishes a framework for measuring service performance. A well-defined SLA can help mitigate risks, enhance communication, and improve the overall relationship between parties involved in a production environment.
The Importance of Production SLA in Business
The significance of a Production SLA can be observed across various facets of a business operation. Here are a few key points illustrating the importance:
- Clarity and Transparency: A Production SLA removes ambiguities by articulating the specifics of what is expected, fostering a clearer understanding between all parties.
- Performance Measurement: With clearly defined metrics, businesses can accurately assess service performance and implement necessary improvements.
- Accountability: SLAs hold parties accountable, ensuring that commitments are met and encouraging high standards of service delivery.
- Risk Management: They help identify potential risks and outline mitigation strategies, contributing to overall business resilience.
- Client Satisfaction: By meeting and exceeding SLA standards, businesses can enhance client satisfaction and loyalty.
Key Components of a Production SLA
A robust Production SLA should encompass several critical components. Each element plays a vital role in ensuring the effectiveness of the agreement. Below are the core components:
1. Service Description
This section provides a detailed description of the services to be supplied under the SLA. It should include what is included and excluded in the service offerings.
2. Performance Metrics
Performance metrics are measurable values that determine how effectively the service is being provided. Common metrics might include response times, throughput, and quality levels.
3. Responsibilities
Clearly outlining the responsibilities of both the service provider and the client is essential. This includes who is responsible for maintaining equipment, managing feedback, etc.
4. Reporting and Review Processes
Establishing regular reporting intervals as well as a clear process for reviewing SLA performance is crucial. This can involve weekly, monthly, or quarterly reviews.
5. Consequences of Non-Compliance
It’s important to specify the repercussions should either party fail to meet the agreements set forth in the SLA. This could include financial penalties or service credits.
6. Amendment Procedures
Over time, business needs may change. Thus, the SLA should contain provisions for how amendments can be made to ensure it remains relevant and realistic.
Crafting an Effective Production SLA
Crafting an effective Production SLA requires careful consideration and collaboration. Here are some recommended steps to ensure your SLA is effective:
1. Engage Stakeholders
Involve all relevant stakeholders in the creation of the SLA, including service providers, clients, and even end-users. This ensures that the needs and expectations of all parties are considered.
2. Define Clear Goals and Objectives
Establish clear, attainable goals that the SLA aims to achieve. This should align with your wider business objectives, particularly within domains like Product Design and 3D Printing.
3. Use SMART Criteria
Goals should be Specific, Measurable, Achievable, Relevant, and Time-bound (SMART). This will help in keeping all parties oriented toward the same targets.
4. Regularly Review and Update
An SLA should not be a static document. Establish a schedule for regular reviews and ensure that it is updated according to any changes in service or business needs.
5. Communicate Effectively
Ensure that there is a strong communication strategy in place for informing all parties of SLA standards, changes, and expectations. Transparency is key to compliance and satisfaction.
Challenges in Managing Production SLAs
While Production SLAs are essential for business operations, managing them can present challenges. Understanding these potential obstacles can help you navigate issues more effectively:
1. Variability in Service Levels
Variations in service levels can arise due to numerous factors such as market demand, production delays, or resource allocation. This can lead to difficulties in meeting SLA expectations.
2. Miscommunication
One hurdle many organizations face is miscommunication regarding SLA terms. It's vital to ensure clear, consistent communication to prevent misunderstandings and foster collaboration.
3. Keeping Up with Technology
As technology rapidly evolves—especially in areas like 3D Printing—keeping your SLA relevant can be challenging. Regular updates and employee training are necessary to stay abreast of changes.
Best Practices for Production SLA Implementation
Implementing a Production SLA effectively requires adherence to best practices. Here are some that can help ensure successful implementation:
1. Pilot Testing
Before rolling out a full SLA, conduct a pilot test with a small project. This enables you to identify weaknesses and make adjustments before a wider implementation.
2. Continuous Training
Regular training sessions for staff involved in SLA management can significantly enhance understanding and compliance. This is especially helpful in dynamic sectors like Product Design.
3. Use Technology Solutions
Leverage technology to track performance against your SLA metrics. Tools and software solutions can automate reporting and monitoring, saving time and reducing human error.
4. Foster a Culture of Accountability
Cultivating a workplace culture that emphasizes accountability can reinforce the importance of meeting SLA standards. Encourage team collaboration and shared responsibility.
Conclusion
In summary, Production SLAs are a cornerstone of effective business operations, especially in fields requiring detailed quality and performance standards. By clearly outlining expectations, accounting for the responsibilities of all parties, and ensuring ongoing communication and review, businesses within the Art Supplies, Product Design, and 3D Printing sectors can greatly enhance their operational efficiency and client satisfaction.
As businesses evolve and grow, so too should their SLAs. By implementing best practices and overcoming challenges effectively, organizations can harness the full potential of Production SLAs, leading to smoother operations and better customer relationships.
For more insights into how SLAs can transform your business processes at arti90.com, be sure to explore our resources on management strategies tailored to the arts and design sectors.