The Importance of Tooling Molds in Metal Fabrication
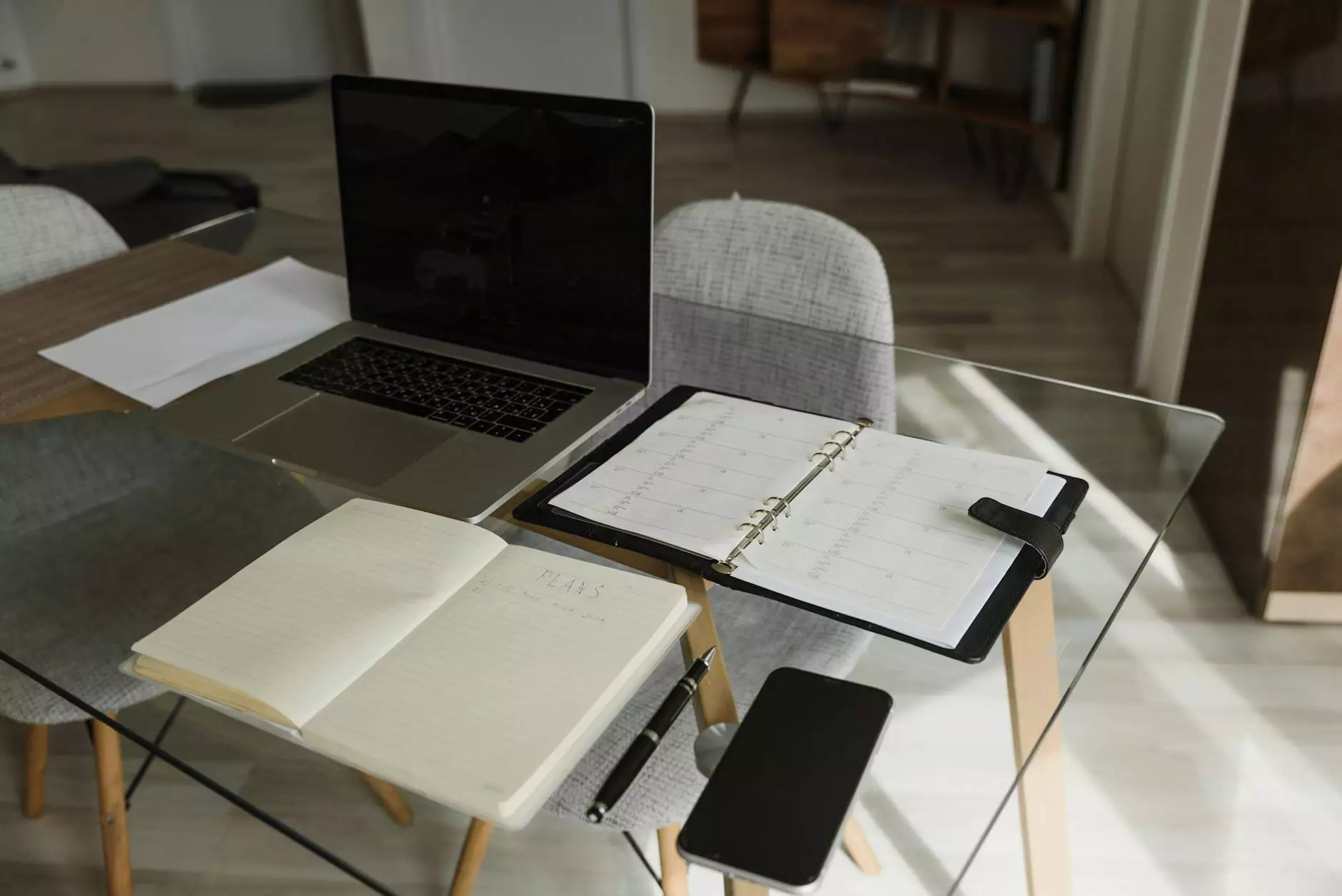
The world of tooling molds is one of creativity, innovation, and precision. In the realm of metal fabrication, tooling molds are a cornerstone of efficiency and quality. This article delves into the various aspects of tooling molds, their applications, benefits, and how they can transform the production processes within the manufacturing sector.
What Are Tooling Molds?
Tooling molds are specialized tools that are used to shape materials, most commonly metals, into desired forms and designs. They serve as templates or dies that guide the manufacturing process to ensure that each part conforms to specific dimensions and tolerances. There are different types of tooling molds, including:
- Injection Molds: Typically used for plastics but evolving into metals.
- Compression Molds: Used for forming materials into shapes by compressing them.
- Rotational Molds: Ideal for creating hollow objects.
- Extrusion Molds: Used to create long shapes by forcing material through a die.
The Role of Tooling Molds in Metal Fabrication
In metal fabrication, tooling molds play a pivotal role in ensuring consistency and scalability in production. They enable manufacturers to achieve:
1. Precision Engineering
The use of high-quality molds ensures that each piece produced is identical. This is paramount in industries such as automotive and aerospace, where even the slightest deviation can result in subpar performance or safety issues. Tooling molds are designed using CAD (Computer-Aided Design) technologies, allowing for meticulous detailing.
2. Increased Efficiency
With tooling molds, the production process is streamlined. Automated systems can utilize these molds for rapid manufacturing, reducing labor costs and time. This efficiency translates into faster output and the capability to meet large orders without sacrificing quality.
3. Cost-Effectiveness
Although the initial investment in high-quality tooling molds may be significant, the long-term savings are substantial. They enable mass production of parts, reducing the cost per unit significantly. Additionally, high-grade molds can withstand thousands of cycles before replacement, providing excellent return on investment (ROI).
The Manufacturing Process of Tooling Molds
The creation of tooling molds involves several steps, each critical to the final product's effectiveness:
- Design: Starting with concept designs created through CAD to establish the mold specifications.
- Material Selection: Choosing the right material for the mold, often steel or aluminum, depending on the requirements.
- Machining: Using CNC (Computer Numerical Control) machines to precisely shape the mold according to design specifications.
- Finishing: Polishing and coating the mold to enhance durability and surface finish.
- Testing: Conducting a series of tests to ensure the mold functions correctly before it goes into production.
Advantages of Using Tooling Molds
Utilizing tooling molds in metal fabrication offers several advantages that enhance the production capabilities of any manufacturing business:
- Improved Quality Control: Consistency in the production process leads to fewer defects.
- Scalability: Easily scales up production with existing molds, thus reducing lead times.
- Design Flexibility: Molds can be adapted or redesigned to accommodate new product lines.
- Enhanced Safety: Reducing the need for manual fabrication processes minimizes workplace accidents.
Industry Applications of Tooling Molds
The versatility of tooling molds enables them to be utilized across various industries:
1. Automotive Industry
In the automotive sector, tooling molds are crucial for creating intricate components such as frames, panels, and engine parts. They facilitate mass production while prioritizing safety and quality standards.
2. Aerospace Industry
Aerospace manufacturing demands precision and reliability. Tooling molds help in the production of lightweight yet durable parts essential for aircraft and spacecraft.
3. Consumer Electronics
With the rapid evolution of technology, tooling molds are increasingly used in the consumer electronics sector to fabricate small, precise components found in devices such as smartphones and laptops.
The Future of Tooling Molds in Metal Fabrication
The future of tooling molds in the metal fabrication industry is promising, driven by advancements in technology:
1. 3D Printing Technology
As 3D printing continues to evolve, hybrid manufacturing processes that combine traditional tooling with additive techniques will emerge, allowing for rapid prototyping and reduced lead times.
2. Smart Manufacturing
Integrating IoT (Internet of Things) with tooling molds will lead to smarter production processes, offering real-time analytics to improve efficiencies and reduce downtime.
3. Sustainable Practices
As companies aim for sustainability, tooling molds will incorporate eco-friendly materials and processes that minimize waste and energy consumption.
Conclusion
In conclusion, tooling molds are an indispensable component of the metal fabrication industry. Their role in enhancing precision, productivity, and efficiency cannot be overstated. By investing in high-quality tooling molds, businesses can significantly improve their manufacturing processes, stay competitive, and meet the growing demands of various industries. Whether you are a small operation or a large-scale manufacturer, embracing the power of tooling molds will undoubtedly pave the way for future growth and success.
For more information on high-quality tooling molds and metal fabrication, visit DeepMould.