The Versatility of Knitted Wire Mesh in Modern Business
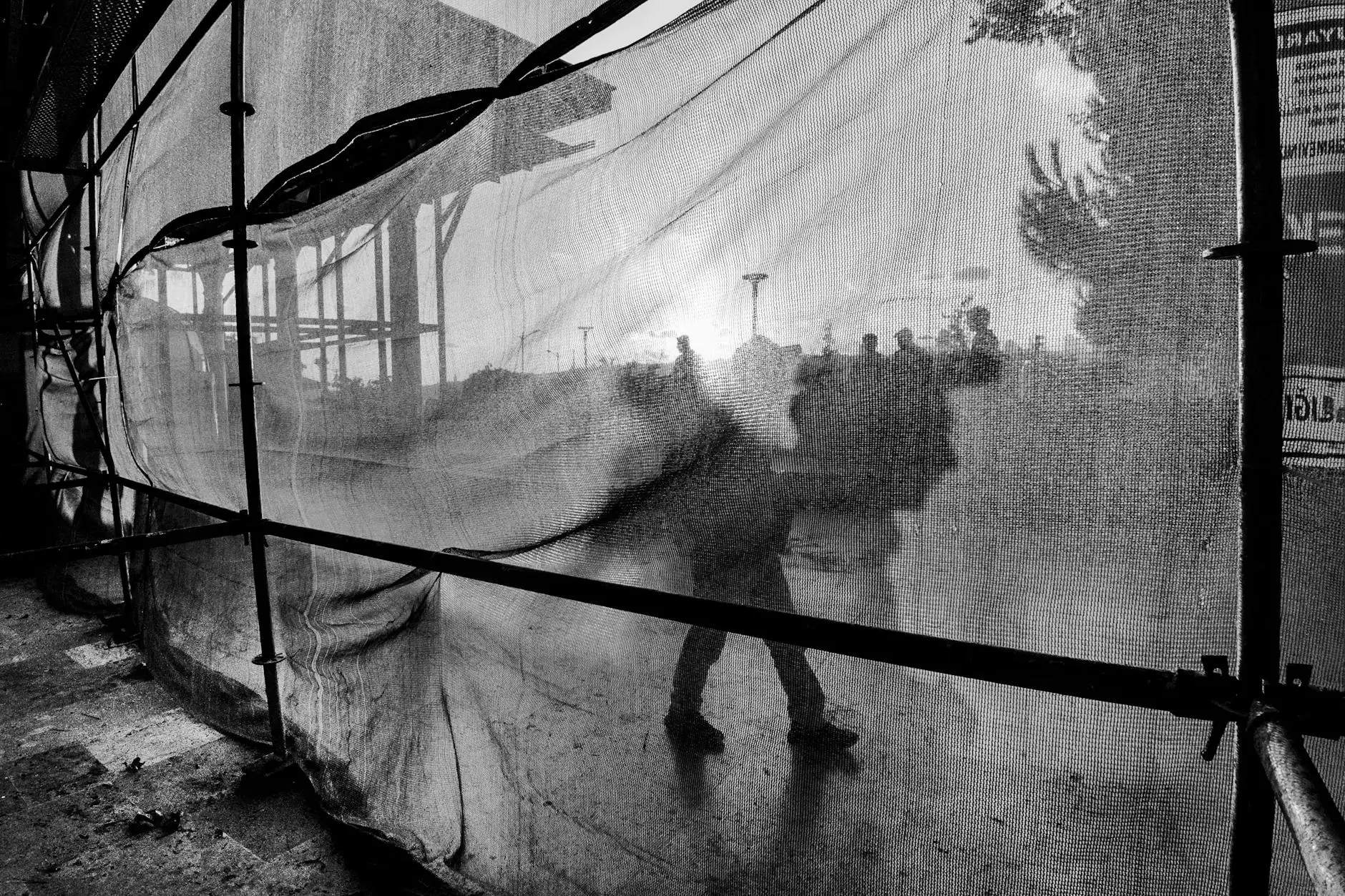
In the ever-evolving landscape of today's industrial operations, materials and processes must adapt rapidly to meet emerging demands. One such innovative material making waves is knitted wire mesh. This article explores the expansive applications of knitted wire mesh, focusing specifically on its use in the electronics and medical supplies industries. We will delve into the unique properties of knitted wire mesh, its benefits, specific applications, and why it is becoming indispensable in modern manufacturing.
Understanding Knitted Wire Mesh
Knitted wire mesh is a type of fabric made from interlacing wire strands. Unlike traditional woven mesh, the knitted variant boasts a higher degree of flexibility, allowing it to accommodate various shapes and sizes without compromising structural integrity. This flexibility is achieved through the unique knitting process, which can produce both fine and coarse mesh depending on the application. The resulting material serves numerous functions, including filtration, support, and decorative applications.
Properties of Knitted Wire Mesh
The distinctive properties of knitted wire mesh make it a preferred choice across various industries:
- Flexibility: The knitted structure allows the mesh to stretch and flex, making it suitable for applications needing dynamic movement.
- Durability: Made from metal or synthetic materials, knitted wire mesh boasts exceptional strength and resistance to wear and tear.
- Lightweight: Despite its durability, knitted wire mesh remains lightweight, making it easy to handle and transport.
- Corrosion Resistance: Many knitted wire meshes are treated to resist corrosion, extending their lifespan in demanding environments.
- Versatility: Available in a variety of materials, including stainless steel, nylon, and brass, knitted wire mesh is customizable for different applications.
Applications of Knitted Wire Mesh in Electronics
The electronics industry has embraced knitted wire mesh for several applications due to its unique properties. Here are some key uses:
1. EMI Shielding
Electromagnetic interference (EMI) can disrupt the functioning of electronic devices. Using knitted wire mesh as a protective shield helps prevent such interference, ensuring that devices operate smoothly. The mesh can be fashioned into enclosures or integrated into device casings.
2. Thermal Management
Effective thermal management is vital in electronics. Knitted wire mesh can assist in dissipating heat from components, enhancing the longevity and reliability of devices. This is especially important in high-performance areas, such as computers and mobile devices, where overheating can lead to device failure.
3. Filters and Screens
In electronic manufacturing, precision is critical. Knitted wire mesh can be utilized as filters and screens in various components, ensuring that contaminants do not affect performance. This quality is essential in creating reliable electronic products that meet rigorous industry standards.
Applications of Knitted Wire Mesh in Medical Supplies
The medical field has also recognized the adaptability of knitted wire mesh. Some notable applications include:
1. Surgical Mesh
Surgical procedures often require materials that are both strong and flexible. Knitted wire mesh is used in various surgical applications, including as a support structure for tissue repair and organ stabilization. Its ability to conform to body contours while providing necessary support makes it an ideal choice.
2. Medical Devices
Knitted wire mesh is integral in the manufacturing of various medical devices, including stents, filters, and catheters. The mesh's malleability allows it to perform effectively in high-precision environments vital for patient health and safety.
3. Protective Equipment
In the context of personal protective equipment (PPE), knitted wire mesh contributes to the creation of durable protective covers that allow for breathability while maintaining structural integrity. This has become increasingly relevant in the ongoing evolution of medical safety standards.
Benefits of Using Knitted Wire Mesh
The adoption of knitted wire mesh in electronics and medical supplies presents numerous advantages:
- Cost-Effectiveness: Its durability and longevity translate to reduced replacement and maintenance costs over time.
- Enhanced Performance: The material's properties allow for improved product performance, whether it's in shielding, filtration, or structural support.
- Customizability: The ability to customize knitted wire mesh for specific applications means businesses can tailor their products to meet precise requirements.
- Sustainability: Many materials used in knitted wire mesh production are recyclable, aligning with modern sustainability initiatives.
Future Trends in Knitted Wire Mesh
As technology progresses, the potential applications for knitted wire mesh are expanding. Some emerging trends to watch include:
1. Smart Materials
The integration of technology into materials is a growing field. Research is underway to incorporate sensors and monitoring devices into knitted wire mesh to track conditions in real-time. This could revolutionize its use in both electronics and medical applications, leading to smarter solutions that enhance product performance.
2. Advanced Coatings and Treatments
Developments in coating technology may lead to more effective and specialized mesh properties. For instance, antimicrobial treatments for medical applications could improve safety and reduce infection risks.
3. 3D Printing Capabilities
As 3D printing technology continues to evolve, there may be potential for utilizing knitted wire mesh within complex structures, creating intricate designs that were previously unattainable. This could lead to innovation in product development across industries.
Conclusion
In summary, knitted wire mesh is a versatile and invaluable material in the realms of electronics and medical supplies. Its unique properties, customizable nature, and adaptability to various applications mark it as a key player in modern business. As industries continue to evolve, the potential for innovation and enhanced performance through knitted wire mesh will likely expand, positioning it as a critical component in the future of manufacturing.
For businesses like Nolato, investing in the capabilities of knitted wire mesh could provide a competitive edge in the market. By understanding its benefits and applications, companies can better serve their clients and drive growth in an increasingly demanding landscape.